Toolbox Talk: Details of the Hazard Communication Standard
Introduction
Ensuring workplace safety is a top priority, especially when dealing with hazardous chemicals. To protect workers, the Occupational Safety and Health Administration (OSHA) has established the Hazard Communication Standard (HCS) 1910.1200. This standard is designed to ensure that employees are fully informed about the potential hazards of the chemicals they work with. It is often referred to as the “Right to Know” law because it grants workers the right to know about the hazards they may be exposed to in the workplace.
The Role of Safety Data Sheets (SDS)
Under OSHA regulations, manufacturers and importers of hazardous chemicals are required to obtain or develop Safety Data Sheets (SDS) for every hazardous chemical they produce or import. These SDSs must then be provided to distributors and employers, ensuring that the information is available to all those who may handle or be exposed to these chemicals.
The SDS must accompany the first shipment of chemicals and be updated within three months if any new and significant information about the chemical becomes available.
The 16-Section Safety Data Sheet
The Safety Data Sheet is an essential tool for hazard communication, providing detailed information about a chemical’s properties, hazards, and handling precautions. Every SDS is structured into 16 sections:
- Identification: Product identifier and supplier information.
- Hazard(s) Identification: All hazards regarding the chemical and required label elements.
- Composition/Information on Ingredients: Chemical ingredients and any trade secret claims.
- First-Aid Measures: First-aid procedures and symptoms of exposure.
- Fire-Fighting Measures: Suitable extinguishing techniques and protective measures.
- Accidental Release Measures: Emergency procedures, protective equipment, and cleanup methods.
- Handling and Storage: Precautions for safe handling and storage.
- Exposure Controls/Personal Protection: Occupational exposure limits and personal protective equipment (PPE) recommendations.
- Physical and Chemical Properties: Characteristics of the chemical, such as its appearance, odor, and boiling point.
- Stability and Reactivity: Chemical stability and potential hazardous reactions.
- Toxicological Information: Health effects and exposure symptoms.
- Ecological Information: Environmental impact, including data on toxicity to aquatic life.
- Disposal Considerations: Safe disposal methods and environmental precautions.
- Transport Information: Shipping classifications and precautions.
- Regulatory Information: Safety, health, and environmental regulations specific to the chemical.
- Other Information: Any other pertinent information, including the preparation and revision dates.
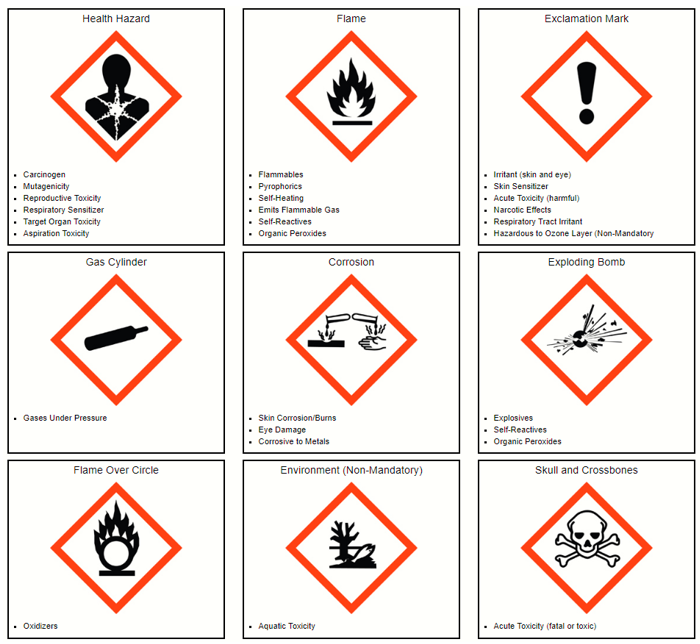
Pictograms and Hazard Symbols
OSHA’s Hazard Communication Standard also requires the use of standardized pictograms to visually communicate the hazards associated with chemicals. There are nine pictograms used in hazard communication:
- Health Hazard: Carcinogen, respiratory sensitizer, reproductive toxicity.
- Flame: Flammables, pyrophoric, self-heating chemicals.
- Exclamation Mark: Irritant, skin sensitizer, acute toxicity, narcotic effects.
- Gas Cylinder: Gases under pressure.
- Corrosion: Skin corrosion/burns, eye damage, corrosive to metals.
- Exploding Bomb: Explosives, self-reactive, organic peroxides.
- Flame Over Circle: Oxidizers.
- Skull and Crossbones: Acute toxicity (fatal or toxic).
- Environment: Aquatic toxicity (non-mandatory in the U.S.).
These pictograms appear on the chemical labels and the SDS to provide a quick visual reference to the type of hazard a chemical-presents.
Employer Responsibilities
Employers have a crucial role in maintaining hazard communication. They must:
- Keep SDS on File for 30 Years: Employers are required to retain Safety Data Sheets for every hazardous chemical used in the workplace for at least 30 years. This ensures that employees and regulators have access to important historical data about chemical exposures.
- Provide Training: Ensure that all employees are trained on the hazards of the chemicals they work with, how to read and understand SDS, and the meaning of the hazard pictograms.
- Make SDS Accessible: SDS must be readily accessible to all employees during their work shifts. Workers should know where to find SDS and how to use them to understand the chemicals they work with.
Summary
Hazard communication is a critical aspect of workplace safety, ensuring that employees are informed about the chemicals they use, and the hazards associated with them. OSHA’s Hazard Communication Standard requires that Safety Data Sheets (SDS) are provided and maintained for every hazardous chemical, structured into 16 sections for comprehensive information. The use of standardized pictograms helps in quickly identifying chemical hazards. Employers are responsible for keeping these SDSs on file for 30 years and ensuring that employees are well-trained and have easy access to this crucial information. By adhering to these guidelines, we can create a safer working environment and reduce the risk of chemical-related incidents.