Toolbox Talk: Respirator Program
Introduction
Under OSHA Standard 1910.134, a respirator program is required whenever air contaminants exceed the Permissible Exposure Level (PEL). Implementing a comprehensive respirator program is essential for protecting workers from hazardous airborne substances. This program must be thorough, regularly updated, and tailored to the specific needs of the work environment.
Key Elements of a Respirator Program
To ensure the safety and effectiveness of respirator use, the following components should be included in your respirator program:
- Medical Evaluation: Before wearing a respirator, each worker must undergo a physician’s examination to confirm their ability to safely use the equipment. This step is critical to ensure that wearing a respirator won’t pose additional health risks.
- Program Implementation and Review: The respirator program must be implemented with a clear plan and regularly re-evaluated, at least annually, to ensure its continued effectiveness and compliance with OSHA standards.
- Written Standard Operating Procedures: Develop detailed written procedures for selecting and using respirators. These procedures should cover everything from initial selection to routine use.
- Fit Testing: Conduct fit testing to ensure that each respirator fits the user properly. This is crucial for effective protection, as a poor fit can compromise the respirator’s ability to filter contaminants.
- Equipment Selection: Select respirators and filters based on the specific atmospheric hazards present in the workplace. Different tasks and contaminants may require different types of respirators.
- Supply and Maintenance: Ensure the availability of necessary cleaning materials, filters, pre-filters, canisters, and spare parts. Proper maintenance is key to ensuring that respirators function as intended.
- Employee Training: Provide comprehensive training on how to use and maintain respirators. Employees should understand the limitations of their equipment and know how to use it correctly.
- Equipment Inspection and Maintenance: Establish procedures for the regular inspection, cleaning, and maintenance of respirators. Maintain records of these activities to ensure ongoing compliance and safety.
- Work-Area Monitoring: Continuously monitor the work area to assess exposure levels and determine the type of respirator needed. This ensures that the selected respirator is appropriate for the current level of contaminants.
- Air Quality Maintenance: For supplied-air devices and self-contained breathing apparatus (SCBA), maintain air quality by ensuring that compressors and other equipment are functioning properly.
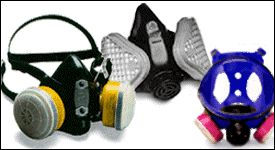
Determining the Need for a Respirator Program
The first step in determining whether a respirator program is needed is to evaluate the level of contaminants in the air and the work processes involved. If contaminant levels exceed the PEL, consider implementing engineering controls to reduce these levels. If controls are not sufficient, respirators become necessary.
Continuous Monitoring and Adaptation
A competent person should regularly monitor the worksite for changes in exposure levels, which may occur due to new chemicals, changes in work methods, or chemical spills. When exposures change, reassess the need for a respirator program and provide additional training if necessary.
Summary
A well-implemented respirator program is vital for protecting workers from harmful airborne contaminants. By following OSHA guidelines, conducting regular evaluations, and providing proper training, you can ensure that respirators are used effectively to keep the air you breathe safe. Remember, respirators are a critical line of defense—learn to select, use, and maintain them properly to safeguard your health.